一、传统编程效率瓶颈如何被突破?
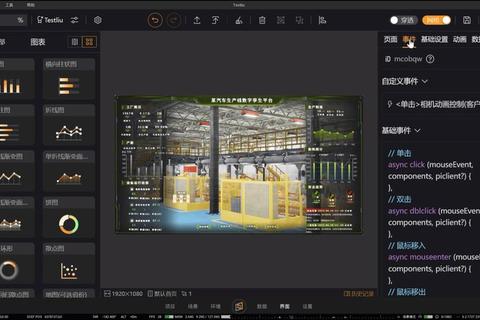
在机械加工车间里,工程师小李正为一批异形齿轮的加工程序头疼——手动编程耗时三天仍未完成刀路验证,而客户要求的交付周期仅剩五天。这种场景折射出传统数控加工的致命痛点:复杂零件编程效率低下,试错成本高昂。
极致灵动Mastercam软件赋能智能数控加工新境界的突破性价值,在深圳某精密模具厂得到印证。该厂承接的汽车涡轮叶片模具订单涉及63组异形曲面,传统CAM软件需要两周编程周期。引入Mastercam 2025的「动态智能刀路生成」功能后,系统通过特征识别自动生成粗加工残留模型,结合AI算法优化切削参数,将编程时间压缩至3天。更令人惊叹的是,软件自带的「刀具路径预测」模块提前检测出两处潜在过切区域,避免价值12万元的毛坯件报废风险。
二、四轴联动加工能否摆脱「高技术门槛」?
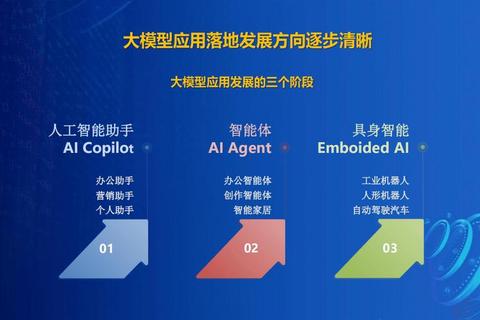
四轴加工曾是企业技术实力的分水岭,某医疗器械企业技术总监王工坦言:「过去培养一个合格的四轴编程员需要两年,现在市场需求倒逼我们必须缩短技术转化周期。」
这一困局在苏州某螺旋槽零件加工企业出现转机。该企业采用极致灵动Mastercam软件赋能智能数控加工新境界的「轴置换法」,将三轴刀路自动转换为四轴联动程序。以直径120mm的医用钛合金螺旋槽加工为例,工程师仅需在二维展开图上绘制槽型轮廓,软件自动完成三维缠绕计算,并生成带A轴旋转补偿的加工路径。对比传统编程方式,加工效率提升40%,更规避了人工计算可能导致的螺旋升角误差。重庆某汽配企业更创造性运用「刀具路径旋转复制」功能,使单个叶轮零件的多角度铣削编程时间从8小时锐减至45分钟。
三、智能优化如何实现「毫米级误差控制」?
航空航天领域对零件精度要求严苛,某卫星推进器喷嘴的轮廓公差需控制在±0.005mm。传统加工依赖老师傅经验微调参数,导致合格率长期徘徊在75%左右。
极致灵动Mastercam软件赋能智能数控加工新境界的「自适应加工」模块,在西安某航天部件厂展现出惊人潜力。系统通过实时读取机床振动、温度、切削力数据,动态调整进给速率和主轴转速。加工某型号火箭燃料阀体时,软件在15处圆弧过渡区域自动启用「光顺连接」算法,使表面粗糙度从Ra1.6提升至Ra0.8,更将刀具磨损量降低27%。东莞某精密注塑模具企业则利用「残料分析」功能,使电极加工余量从0.3mm精确控制到0.1mm,每年节省紫铜材料成本超80万元。
破局者的发展路径启示
从这三个维度可见,智能制造不是简单的设备升级,而是软件算法与工艺经验的深度融合。对于企业而言:
1. 优先布局复合型人才培养:建议技术团队每年完成40学时以上的Mastercam专项培训,重点掌握「智能刀路」与「机床仿真」模块
2. 建立加工参数数据库:将已验证的切削参数、刀具补偿值存入软件数据库,新零件编程时可调用相似工艺模板
3. 推行「虚实结合」验证机制:重要零件必须经过软件的全流程仿真加工,通过「碰撞检测」和「材料去除分析」规避实际加工风险
当重庆某民营企业用Mastercam完成首套航天级零件的自主加工时,总经理感慨:「这不仅是技术升级,更是思维模式的革新。」在智能制造的赛道上,极致灵动Mastercam软件正重新定义数控加工的价值边界,让每个机械加工企业都有机会站上精密制造的新高地。
相关文章:
文章已关闭评论!