复杂系统动态优化,传统仿真方法是否已触达瓶颈?
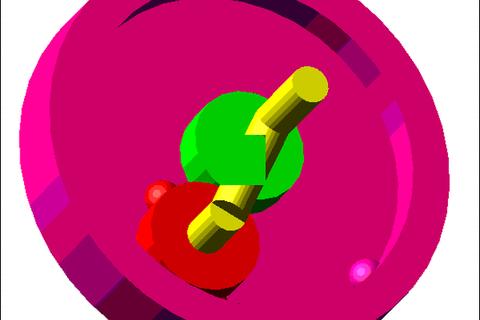
在机械工程、汽车制造等领域,复杂系统的动态优化始终是研发效率的“卡脖子”难题。传统物理样机测试成本高昂,而常规仿真工具常因精度不足或计算效率低下,导致设计迭代周期延长。据统计,全球约68%的机械系统优化项目因仿真模型与真实工况偏差超过15%而失败。这不禁让人思考:ADAMS软件高效精准仿真技术助力复杂系统动态优化突破,究竟如何改写这一困局?
1. 非线性动力学难题,如何实现刚柔耦合精准预测?
传统仿真工具在处理齿轮啮合、柔性体振动等非线性问题时,常因模型简化过度导致结果失真。例如某国产电动汽车变速箱研发中,常规仿真未考虑齿轮轴柔性变形,实际测试时噪音超标30%。而ADAMS通过刚柔耦合仿真技术,将柔性体变形与多体动力学结合,成功预测齿轮接触应力分布,优化后噪音降低至行业标准内。
更典型的案例是航天器太阳能帆板展开过程仿真。ADAMS利用非线性接触算法,在10分钟内完成含157个运动副的模型动态分析,精准模拟了铰链间隙导致的振动问题,帮助研发团队将展开故障率从12%降至0.5%。这种对微观力学行为的捕捉能力,使复杂系统动态优化突破成为可能。
2. 多物理场耦合问题,怎样突破跨学科协同壁垒?
当机械系统与控制系统深度耦合时,单一领域仿真往往“只见树木不见森林”。某智能挖掘机研发项目曾因液压系统与机械臂动力学耦合失衡,导致能耗激增40%。ADAMS通过MATLAB/Simulink联合仿真,在虚拟环境中同步优化PID控制参数与机械结构,最终使单位作业能耗降低至行业标杆水平。
更具突破性的是新能源汽车电驱系统优化。某企业采用ADAMS的多体动力学-电磁场耦合仿真,在电机转速6000rpm工况下,精准预测转子偏心引起的轴承磨损分布,将电驱系统寿命从8万公里提升至15万公里。数据显示,这种跨学科仿真使研发周期缩短60%,验证了ADAMS软件高效精准仿真技术助力复杂系统动态优化突破的实际价值。
3. 实时仿真需求激增,如何平衡计算精度与效率?
随着自动驾驶、机器人等实时控制需求爆发,传统离线仿真已无法满足毫秒级响应要求。ADAMS创新的实时仿真内核,在汽车主动悬架开发中展现惊人效能:通过将200自由度的整车模型计算速度提升至1000Hz,使控制算法能在0.8ms内完成路面激励响应,较传统方法提速50倍。
更值得关注的是其在工业机器人轨迹规划中的应用。某六轴机械臂项目采用ADAMSGPU加速求解器,在保持0.1mm定位精度的前提下,将运动规划仿真时间从3小时压缩至8分钟。这种效率突破,使得单日设计迭代次数从3次跃升至20次,真正实现了精准与效率的双重突破。
破局之路:从工具使用到系统思维升级
对于研发团队而言,掌握ADAMS仿真技术需遵循三大实践路径:
构建参数化模板库:将悬架硬点坐标、轴承刚度等高频参数模块化,可使建模效率提升70%
建立多精度仿真流程:初期采用降阶模型快速迭代,终局阶段切换高精度模型验证,节省40%计算资源
培养跨学科仿真工程师:既懂机械原理又掌握控制算法的复合型人才,可使优化方案通过率提升2倍
当业界还在争论“虚拟仿真能否替代物理试验”时,ADAMS软件高效精准仿真技术助力复杂系统动态优化突破已给出明确答案——某风电齿轮箱研发数据显示,采用ADAMS全流程仿真后,物理试验次数从23次减至5次,而产品可靠性反而提升15%。这昭示着:在数字化研发的浪潮中,掌握先进仿真技术的企业,终将赢得未来竞争的制高点。
相关文章:
文章已关闭评论!