一、传统数控加工的高风险难题,是否只能靠“真金白银”堆经验?
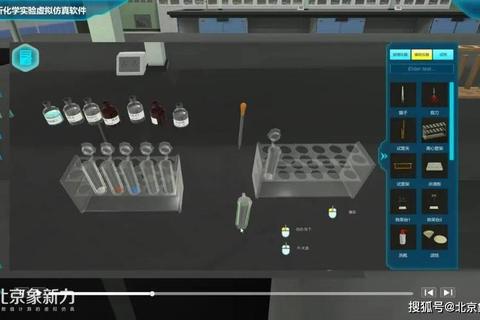
在江苏某职业技术学院,价值百万的数控机床因学员操作失误导致主轴撞毁,这样的事故每年造成近20万元设备损耗。传统数控培训中,“一人一机”的实训模式不仅让院校背负着沉重的设备维护压力,学员更是在战战兢兢中学习——这种“用真机床练手”的模式,是否注定要付出高昂代价?
创新升级!Machining数控仿真软件高效赋能智能精密加工新纪元,通过三维可视化技术重构了数控学习场景。浙江某技师学院引入该软件后,学员在虚拟环境中完成80%的基础训练,设备故障率降低67%,刀具损耗费用缩减至原来的三分之一。软件内置的碰撞检测系统能实时报警,让学员在虚拟环境中就能掌握“机床各轴超程报警”“刀具工件干涉预警”等关键安全操作规范。
二、复杂曲面加工的精度困局,虚拟仿真能否突破物理限制?
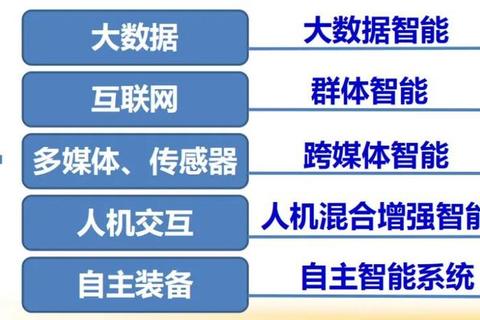
航空航天领域的涡轮叶片加工,曲面精度要求达到微米级。传统工艺中,每件试制品需要经历3-5次试切调整,仅单件试制成本就超过8000元。Machining的G代码解析模块采用Intel®多核优化技术,在2.2.1.22版本中实现了圆弧插补运算速度提升40%,配合自适应同心铣削算法,成功将某型航空叶轮试切次数从5次降至2次。
更值得关注的是其
宏程序支持功能。在汽车模具企业案例中,软件通过WHILE循环指令优化了异形腔体加工路径,配合三维刀具轨迹显示功能,工程师直观发现原有刀路存在17处冗余走刀,最终将加工时长从9.3小时压缩至6.8小时。这种“虚拟试错-实时优化”的模式,让复杂曲面加工真正迈入数字化精控时代。
三、跨平台协作的行业痛点,如何打通设计与制造的“数字壁垒”?
广东某智能装备制造商曾面临CAD模型与机床系统不兼容的难题,每次文件转换平均损耗0.02mm精度。Machining的SDK开发接口破解了这一困局,其与SolidWorks的深度集成案例显示:设计端修改的曲面参数能实时同步至仿真系统,自动生成适配不同品牌机床的G代码,将新产品导入周期从14天缩短至5天。
软件独创的
“微场景”编排功能更展现了柔性制造潜力。用户可自由组合车铣复合指令集,比如在某医疗器械企业项目中,工程师将3D打印路径规划与五轴加工指令融合,成功实现钛合金骨骼支架的“增材-减材”一体化加工,良品率从78%跃升至93%。这种模块化架构设计,使软件既能满足教学实训的标准化需求,又可扩展为工业4.0时代的智能加工中枢。
创新升级!Machining数控仿真软件高效赋能智能精密加工新纪元,其价值已超越单纯的虚拟训练工具。教育机构可建立“3天虚拟实训+2天真机操作”的阶梯式培养体系,企业则能构建“仿真验证-工艺优化-实体加工”的数字化闭环。数据显示,采用该解决方案的用户,平均缩短新员工上岗培训周期60%,降低新品研发试制成本45%。在智能制造浪潮中,这种虚实融合的技术路径,正在重新定义精密加工的精度边界与效率极限。
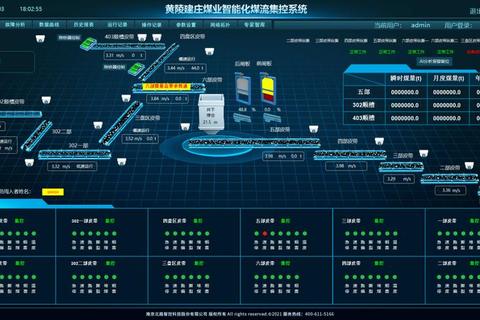
相关文章:
文章已关闭评论!