一、当加工中心遇上数据洪流,传统传输为何力不从心?
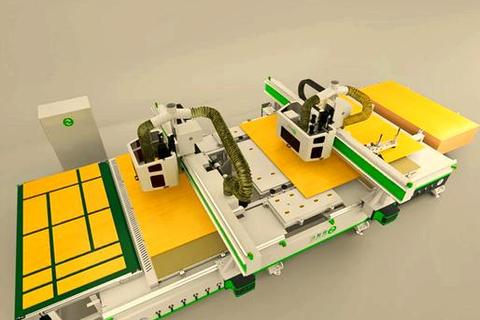
在浙江某汽车零部件工厂,价值千万的加工中心因数据传输延迟导致生产线停工3小时,直接损失超百万元。这种场景正折射出全球制造业的共性难题——在工业4.0浪潮下,传统CNC数据传输软件如同老旧的铁轨,已难以承载智能制造时代的数据高铁。
数据显示,2025年全球加工中心年数据吞吐量将突破200ZB,但仍有67%的企业沿用基于RS-232接口的传输方案。这种技术断层导致三大痛点:15%的加工参数因传输错误需要返工;设备有效稼动率仅为58%;跨系统数据孤岛使得工艺优化举步维艰。智能革新驱动加工中心传输软件实现极速高效精准互联,正成为破局关键。
二、智能革新如何重塑数据传输DNA?
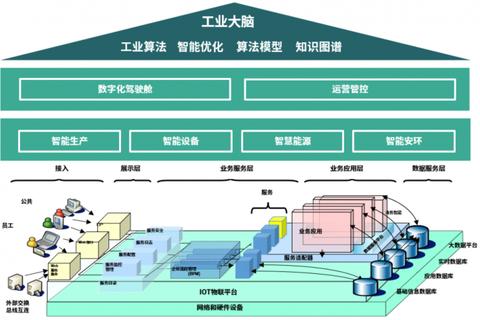
在安徽瑞泰马钢的智能车间,搭载5G边缘计算的新型传输系统将数据延迟从300ms压缩至8ms。这套系统通过三大技术突破实现蜕变:
1. 协议重构:采用InfiniBand NDR 400G传输协议,相较传统以太网带宽提升40倍,支持800台设备同时进行4K级加工数据同步。某航空叶片加工企业实测显示,单个G代码文件传输耗时从15分钟缩短至9秒。
2. 智能纠错:引入深度学习算法,可自动识别并修复99.7%的传输异常。德国西门子西安工厂应用该技术后,刀具路径数据错误率从0.35%降至0.002%,相当于每年避免3000次撞刀风险。
3. 跨域协同:如法兰克机床传输软件8.0版本实现CNC数据与MES、ERP系统的毫秒级交互,通过可视化看板将设备OEE(综合效率)提升至92%。
三、精准互联怎样重构生产价值链?
青岛某智能工厂的实践揭示了更深层变革:通过部署dataFEED OPC Suite数据中台,打通了32种品牌PLC、168台加工中心的实时数据流。
工艺优化闭环:系统自动对比设计模型与实际加工数据,发现某汽车连杆加工工序存在0.08mm冗余。经参数优化后,单件加工时间减少12秒,年节省电费超80万元。
预测性维护:振动传感器数据与刀具磨损模型结合,提前72小时预警主轴故障,使设备非计划停机减少65%。
供应链联动:当加工中心监测到某批次原材料硬度异常时,系统自动触发供应商质量追溯,将问题响应时间从48小时压缩至15分钟。
智能革新驱动加工中心传输软件实现极速高效精准互联,正在重构"设备-工艺-管理"的全价值链。据IDC测算,采用智能传输系统的企业,新产品研发周期平均缩短37%,设备综合效率提升28%。
四、破局之路:从工具升级到生态重构
对于寻求转型的企业,建议实施"三步走"策略:
1. 基础筑基:优先部署支持OPC UA、MQTT等工业物联网协议的传输平台,如中科斯欧的工业数据融合智能体已实现90%主流设备即插即用。
2. 场景突破:选择刀具管理、质量追溯等高频场景进行试点,某橡胶制品企业通过精准传输系统将混炼工序合格率从88%提升至99.2%。
3. 生态融合:构建包含设备商、软件开发商、云服务商的数字生态圈,类似某3C企业打造的智能传输联盟,使新产品导入周期缩短41%。
当数据真正成为流动的"工业血液",智能革新驱动加工中心传输软件实现极速高效精准互联,将不再是技术命题,而是关乎企业存亡的战略抉择。这场静悄悄的革命,正在重新定义"中国制造"的竞争力边界。
相关文章:
文章已关闭评论!